فولاد کربنی API 5L-بررسی خوردگی توأم با تنش (SSC) در ناحیه HAZ در خطوط انتقال گاز ترش
فولاد کربنی API 5L- فولاد ضد زنگ آستنیتی 316L-بررسی خوردگی توأم با تنش (SSC) در ناحیه haz در خطوط انتقال گاز ترش
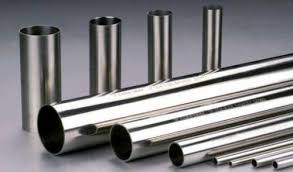
در این تحقیق با هدف بررسی ترک های احتمالی که ایجاد شد. با بکار گیری از الکترودهای متفاوت و در نظر گرفتن متغیرهای عملیاتی. با ساختن قطعات آزمایش طبق استانداردهای مرتبط و از جنس لوله های مورد مصرف در مسیر گازهای ترش. که فولاد کربنی نوع API 5L و فولاد ضد زنگ آستنیتی نوع 316L می باشند. در پی یافتن میزان مقاومت به خوردگی تنشی و ترک های احتمالی به که به وجود آمد در ناحیه متأثر از حرارت جوش (HAZ). و در نتیجه کشف راه کاری مناسب به منظور حداقل رساندن این فرایند هستیم.
بررسی های میکروسکوپی بر روی نمونه ها در ناحیه تأثیر گذار گرمایی نشان می دهد. که اکثر نمونه ها در این ناحیه مستعد به تشکیل ترک های ناشی از خوردگی تنشی بوده. و ترکیبی از دو حالت ترک های میان دانه ای و بین دانه ای هستند. همچنین با افزایش میزان سولفور موجود در گاز ترش، ترک های میان دانه ای بیشتر و تأثیر گذارتری در نمونه ها مشاهده شد. نتایج نشان می دهد که کمترین ترک ها در استفاده از الکترودهای همسان با فلز پایه. از نظر ترکیبات شیمیایی و همچنین الکترودهای با درصد نیکل بالاتر نسبت به فلز پایه بوده است. همچنین تراکم ترک با توجه به مدت آزمایش 120 روز، و میزان سولفور در بیشتر نمونه های تحت تنش افزایش می یابد.
در ترک های ناشی از خوردگی تنشی دو نوع ترک کلی نمایان است. که شامل ترک های بین دانه ای، که در طول مرز دانه ها حرکت می کند، و ترک های میان دانه ای. که از داخل آنها عبور می کنند، می باشد.
نوع ترک بستگی به محیط خورنده و ساختمان فلز دارد. ترک خوردن معمولاً در جهت عمود بر تنش مورد اعمال اتفاق می افتد. هر فلز جهت وقوع ترک های ناشی از خوردگی تنشی نیاز به یک حد تنش کششی خاص و محیط خورنده ویژه دارد. به گونه ای که اگر تنش کششی اعمالی زیر این حد تنش خاص باشد، این نوع ترک ها رخ نمی دهند. در واقع هر چه استحکام کششی افزایش یابد مقاومت به ترک های ناشی از خوردگی تنشی نیز بهبود می یابد.
طراحی و انجام آزمایش
همانطوری که قبلاً اشاره شد هدف اصلی، بررسی رشد ترک در نواحی جوش در خطوط لوله انتقال گاز ترش در پالایشگاه ها می باشد. و با توجه به اینکه جنس این لوله ها طبق بررسی های مورد انجام. از منابع و نقشه های موجود از جنس فولاد کربنی نوع API 5L و فولاد آستنیتی نوع 316L می باشد، بدیهی است. که نمونه های انتخابی با توجه به فریضه اصلی که جنس آلیاژ ثابت است. باید از جنس فولاد با استاندارد NACE MR0175 و با همان خاصیت باشند.
بنابراین پس از انتخاب نوع فولاد، موضوعی که مطرح است. این است که بهترین راهکار و استاندارد جهت ساخت نمونه. که بتواند نتایج قابل قبولی را ارائه نماید. متناسب با تحقیق و تأیید شده انجمن ASTM هست. و راه حلی بسیار خوب برای تحلیل ترک ناشی از خوردگی تنشی باشد.
با توجه به اینکه در این استاندارد ابعاد و دیگر مشخصه های طراحی به طور کامل بیان شد. بنابراین تصمیم بر آن شد که طبق استاندارد فوق چندین نمونه از نمونه های مورد اندازه گیری. برش شوند و سایر عملیات ماشین کاری از قبیل سوراخ کاری، جوشکاری، خم کاری و غیره بر روی آنها انجام گیرد. حال نمونه های تولیدی، جهت قرار گیری در محیط واقعی برای بررسی های بعدی مهیا می شوند. جزئیات بیشتر نحوه ساخت نمونه ها و همچنین ترکیبات و نوع محیط در قسمت بعد بیان می شود.
نمونه آزمایش
پس از مشخص شدن نوع فولادها که همان فولاد کربنی نوع API 5L و فولاد آستنیتی نوع 316L. با ترکیبات شیمیایی طبق جدول شماره (1) و شماره (2) از جنس لوله و مخازن در شرایط واقعی می باشند. حال بررسی کار در شرایط آزمایشگاهی و تطابق آن با حالت واقعی. نمونه های آزمایشگاهی با استفاده از استاندارد ASTM-G30 تهیه گردیدند. Standard Practice for making and using U-Bend Stress Corrosion test Specimens. این استاندارد، دستورالعمل ساخت و استفاده نمونه های خم U. مانند را برای ارزیابی ترک های ناشی از خوردگی تنشی در بین فلزات بیان می کند.
نمونه U معمولاً یک تسمه مستطیل شکل با اندازه های مشخص بکار می گیرند. که به میزان 180 درجه دور یک جسم شعاعی مشخص خم گردیده. و در هنگام آزمایش خوردگی تنشی به همین حالت کرنش ثابت باقی می ماند.
نمونه های تحت تنش سپس در محیط قرار داده شده و تا زمان ترک که ایجاد می شود، بدین صورت قرار می گیرند. این نمونه های U مانند ممکن است که برای هر آلیاژ فلزی بکار روند. منوط به اینکه به اندازه کافی خاصیت چکش خواری داشته باشند. تا بتوان آنها را به شکل U بدون هیچ گونه ترک مکانیکی، درآورد.
در اکثر موارد جهت ساخت این نمونه ها از نوار یا ورق فلزی استفاده می کنند. اما آنها میتوانند توسط مفتول هاف ورق های نازک فلزی و یا قطعات جوشکاری شده یا ماشینکاری شوند و نیز به کار روند. از مزیت های عمده این روش ساخت نمونه. ساده و اقتصادی بودن آنها می باشد. و برای تشخیص اختلاف های بزرگ بین مقاومت ترک های ناشی از خوردگی تنشی از : الف) فلزات مختلف در محیط های یکسان. ب) یک فلز در شرایط متالورژیکی متفاوت در یک محیط یکسان، ج) یک فلز در چندین محیط، بسیار مفید و مناسب می باشد.
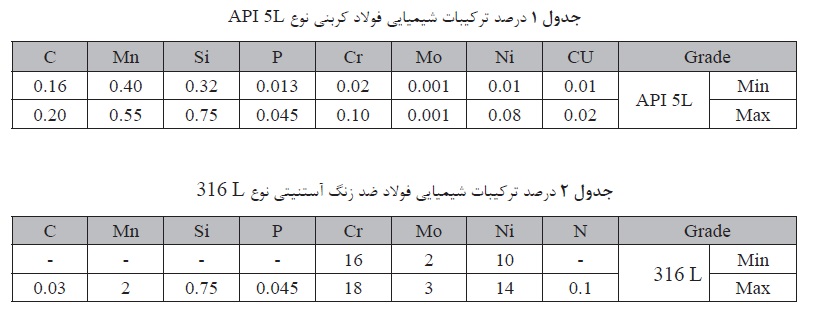
در اینجا قبل از آزمایش. خلاصه ای از تأثیر ترک با توجه به ظرفیت تحمل فشار در خطوط لوله انتقال گاز به صورت تئوریکی نکاتی را یادآوری می نماییم.
ابتدا دو حالت ناشی از دو شکل عمق محدود و راه به در را بررسی می کنیم. نمودارهای ظرفیت تحمل فشار در خطوط لوله نفت و گاز بر حسب عوامل مختلف نشان دهندۀ تأثیر هر یک از این عوامل می باشد.
حالات مختلف عبارتند از :
ترک راه به در
فرض کنیم در راستای محور لوله یک ترک راه به در به طول 2C ایجاد شده است. فولیس (Folias) با تعریف پارامتری به نام و با رابطۀ عددی بی بعد به دست آورد.
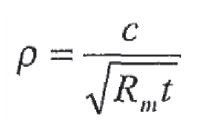
که در این رابطه:
P: طول نرمالیزه شدۀ ترک
C: نصف طول ترک
Rm: شعاع میانی سطح مقطع لوله (میانگین شعاع داخلی و شعاع خارجی)
t: ضخامت دیوارۀ لوله
فولیس (Folias) سپس رابطه زیر را برای تحمل فشار ارائه نمود.
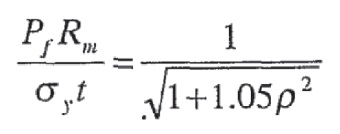
که در آن:
Pf: فشار واماندگی خط لوله
Y: تنش تسلیم می باشد
یک سال بعد اردوگان (Erdogan) رابطه ای دیگر پیشنهاد نمود که تطابق خوبی با رابطه فولیس (Folias) داشت:

ترک عمق محدود
حال فرض کنیم ترک حالت قبل راه به در نباشد، شکل شماره (1)، بلکه عمقی به اندازۀ a داشته باشد. کارتر (Carter) پیشنهاد داد که ظرفیت تحمل فشار با رابطۀ زیر محاسبه گردد.
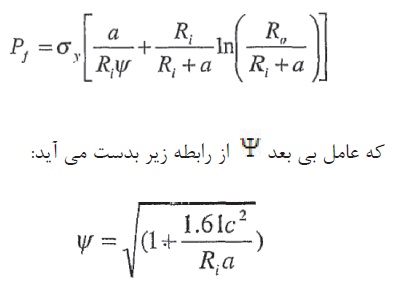
در روابط بالا Ri و Ro به ترتیب شعاع های داخلی و خارجی لوله هستند. کارتر (Carter) بر خلاف روشی که فولیس (Folias) و اردوگان (Erdogan) به کار بردند. عبارت سمت چپ تساوی را بر حسب کسر بیان نکرد، در حالیکه پیش از او اوینگ (Ewing). ظرفیت تحمل فشار لولۀ دارای ترک عمق محدود را به صورت زیر بدست آورده بود:
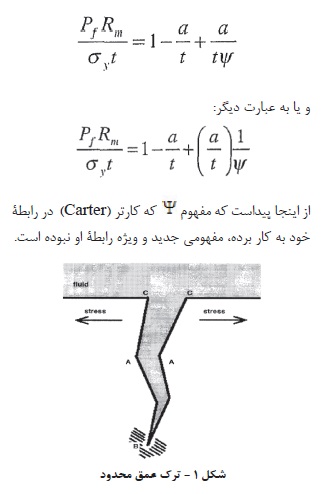
نحوه آزمایش و آزمایشات متالوگرافی
ابتدا طبق جدول استاندارد ASTMM تعداد 12 عدد تسمه فلزی از جنس فولاد کربنی API 5L و فولاد آستنیتی ضد زنگ نوع 316L تهیه نموده. و دقیقاً در خط تقارن عرضی تسمه برش زده و باید آنرا به دو قسمت مساوی تقسیم نمود. هدف از این کار انجام جوشکاری بر روی محل برش تسمه، جهت اتصال مجدد دو نیمه به یکدیگر. و همچنین موضوع دیگر در این محدوده از اتصال جوش باید تحقیق انجام پذیرد. نمونه ها توسط 12 مدل الکترود مختلف جوشکاری سپس تحت عملیات تنش زدایی PWHT قرار داده شدند.
توسط پیچ و مهره نمونه ها تحت تنش نرمال قرار گرفتند تا شرایط یکسان تنش ثابت در خطوط لوله بر روی نمونه ها اعمال شود. جهت ادامه آزمایش 6 عدد از نمونه های تحت تنش (3 نمونه فولاد کربنی و 3 نمونه فولاد آستنیتی). را در محیط کار و مسیر کمکی خط لوله گاز ترش با میزان سولفور 2000PPM بصورت ثابت نصب کرده. و شیر منتهی به این خط را مقداری باز نموده. تا نمونه ها در معرض سیال هیدروکربنی قرار گیرند.
6 نمونه دیگر (3 نمونه فولاد کربنی و 3 نمونه فولاد آستنیتی) در همان شرایط ولی با میزان سولفور 500ppm تحت تنش در مسیر گاز ترش قرار گرفتند. تا پایان آزمایش که 120 روز طول کشید، نمونه ها چهار بار مورد بررسی قرار گرفتند و مورد مقایسه قرار گرفتند.
بعد از اتمام مدت زمان در که در نظر می گیرند، نمونه ها از سیال گازی خارج می نمایند. و پس از شستشو هر نمونه را به ترتیب در محدوده متأثر از حرارت جوش و فلز جوش، توسط اره، برش عرضی می دهند. سپس نمونه ها جهت آزمایش متالوگرافی، علامت گذاری می گردند و تک تک در نواحی مورد نظر توسط سوهان های سایشی متفاوت (آج بزرگ و کوچک) تا سطح صاف و صیقلی سوهان کاری شدند. در مرحله بعد ابا استفاده از سنگ سنباده یا کاغذ سنباده سطوح را کاملاً صیقلی کرده. و در نهایت توسط پاشش محلول AL203. اکسید آلومینیوم با اندازه دانه 0/050 میکرون توسط دو محلول مخصوص بوسیله یک پارچه نرم صیقل می دهند. و توسط میکروسکوپ در مقیاس های مختلف مورد بررسی قرار گرفتند. و عمل عکس برداری جهت بررسی ریزساختارها و مرز دانه ها و ترک های احتمالی انجام گرفت.
تجزیه و تحلیل
ریخت شناسی ترک
در این مطالعه و بررسی، تعدادی از ترک ها در سطح که برش می خورد نمونه ها آزمایش U شکل. در ناحیه متأثر از حرارت جوش انتشار پیدا کردند. تمامی عوامل را که برای تشکیل ترک ناشی از خوردگی تنشی لازم است، در این مطالعه مؤثر بوده اند. بعلاوه مشاهدات میکروسکوپی نشان می دهند. که در این نمونه ها، ترک ها به دو صورت بین دانه ای و میان دانه ای گسترش می یابند.
شکل شماره (2) نمایان گر این مطلب می باشد. اما از لحاظ کمی انتشار ترک های میان دانه ای بیشتر و وسیع تر بوده است. مانند شکل (3) که این دلیلی بر مستعد بودن اینگونه فولادهای زنگ نزن آستنیتی. به ترک های میان دانه ای از روی مرزدانه ها و دانه ها عبور می کنند. در صورتی که ترک های بین دانه ای در طول مرز دانه ها عبور می نمایند. شکل (4) ترک های بین دانه ای را نشان می دهد.
بعضی از ترک های میان دانه ای دارای یک نوک هستند. و معمولاً از خود یک مسیر خوردگی مشهود در طول خط شکست نشان می دهند. به نظر می رسد که نسبت زمان تأخیر قبل از تشکیل ترک. با شروع حفره ها و مسیرهای خوردگی که از قبل موجود است وجود دارد. همچنین بیشتر ترک ها دارای مسیرهای انشعابی هستند و از مسیر اصلی خود انحراف یافتند.
یک تغییر محلی در ریزساختار در جلوی نوک ترک می تواند باعث انحراف ترک گردد. زیرا تغییر مسیر و انحراف ترک به ساختار ریزدانه ای مرتبط است. در دانه های آستنیتی ترک ها به هر دو صورت میان دانه ای و بین دانه ای رشد می کنند. و یک تغییر مسیر در ریزساختارف بعنوان مثال وجود یک ناحیه وسیع آستنیتی نسبت به یک ناحیه فریتی. در جلوی نوک ترک باعث انحراف مسیر ترک می گردد.
پارامترهای جوشکاری
در نمونه های آزمایش مشخص گردید که همه آنها در ناحیه تأثیر پذیر گرمایی جوش (HAZ) مستعد به تشکیل ترک بوده. و حتی حفره های متعدد نیز ایجاد می شود. لذا پارامترهای فوق در تشکیل این ترک ها مؤثر بوده اند. با توجه به این که همه این پارامترها برای نمونه ها یکسان در مد نظر قرار گرفتند. استفاده از آلیاژهای کم کربن (شاخه L). در الکترودها خطر حساس سازی را بوسیله کند کردن واکنش، و به حداقل رساندن رسوب کاربید، به حداقل می رساند. حتی تنشهای پسماند در ناحیه متأثر از حرارت نیز ممکن است باعث تشدید واکنش تشکیل رسوب گردد.
فولاد کربنی API 5L
همچنین شکل گرده جوش به صورت محدب انتخاب گردید که در این روش احتمال تشکیل ترک در هنگام سرد شدن ناچیز و کمتر است. شکل شماره (5) ساختار میکروسکپی جوش را نشان می دهد. نسبت پهنا به عمق نیز 2 به 1 در مد نظر قرار گرفت که این مقدار باعث تشکیل ترک در امتداد سطح نمی شود. در فرآیند جوشکاری از جریان جوش بالا و سرعت های جوش پایین که باعث کاهش میزان سردکاری می شود. و همچنین احتمال تشکیل ترک های زیر جوشی و پای جوش را به حداقل می رساند، نیز استفاده گردید.
بررسی نقش الکترود و ترکیبات آلیاژی
در این بررسی از 12 نمونه الکترود مختلف، طبق جداول شماره (3) و (4) در شاخه های فولادی آستنیتی و کربنی بکار رفت. که قطر این الکترودها به نسبت ضخامت قطعه مناسب هستند (25 میلی متر). و هر کدام با توجه به ترکیبات خاص خود تأثیر مفید و یا نامطلوب در عملکرد جوشکاری داشته اند.
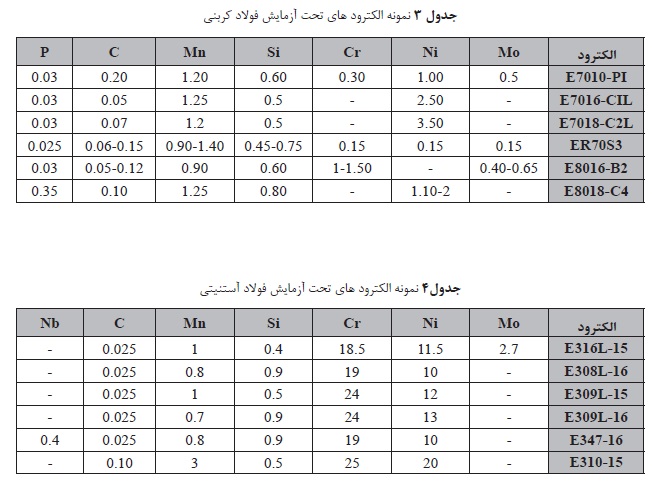
جدول شمار (5) و (6) با توجه به نوع الکترود ها در محیط های مختلف با میزان سولفور متفاوت در گاز ترش. مشخصات ترک های موجود نمایان است. بعنوان مثال الکترود E310-15 که در دو نمونه آزمایشی از آن به عنوان فلز جوش به کار رفت. دارای درصد نیکل بیشتری در حدود 20% نسبت به فلز پایه می باشد. در نتیجه جوش تولیدی به دلیل دریافت نیکل از فلز جوش در اینجا محتوی هیچ فریتی در محل ریشه جوش نیست. در نتیجه عدم وجود فریت سبب ایجاد حساسیت جوش و ناحیه HAZ آن به ترک خوردگی می گردد.
معمولاً فلز جوش در فولادهای زنگ نزن آستنیتی یک ساختار ترد با 2 الی 10 درصد فریت در شبکه آستنیتی دارند. و در الکترود E7010-PI بیشترین نوع ترک میان دانه ای و بین دانه ای مشاهده گردید. که دلیل اصلی آن مقاومت ضعیف این نوع الکترود نسبت به تنش و میزان ترکیب زیاد کربن در آلیاژ این الکترود. نسبت به سایر الکترودها می باشد. اشکال (6) و (7) نشانگر این مدعی است.
فولاد کربنی API 5L
کمترین ترک در نمونه با الکترود E316L-15 به تشکیل می یابند. که این می تواند به دلیل همخوانی بسیار نزدیک درصدی آلیاژی فلز جوش و فلز پایه باشد. این پدیده در مورد فولادهای شاخه 304 نیز صادق است. زیرا در عمل اینگونه فولادها را با الکترود آستنیتی E-308 جوشکاری می کنند. همچنین در نمونه جوشی با الکترودو E309L-16 در نمونه تنش ثابت، ترک های کمتری مشاهده گردیده است.
و این می تواند به دلیل درصد نیکل و کروم بالای این الکترود باشد. در هر حال بنظر می رسد که تطابق آلیاژی فلز پایه و فلز جوش. یکی از عوامل مؤثر بهبود در ترک های مورد تشکیل ناشی از خوردگی تنشی می باشد. همچنین درصد ترکیبات آلیاژی الکترودها مانند مقدار نیکل بالا یا کربن پایین. یکی از عوامل مهم در جلوگیری از ترک های ناشی از خوردگی تنشی می باشد.
تنها نمونه ای که ترکی در آن نمایان نگردید، نمونه مورد جوشکاری با الکترود ER-70S3 می باشد. که بالاترین نوع مقاومت و بیشترین استحکام را تحت تنش در محیط خورنده از خود نشان داده است.
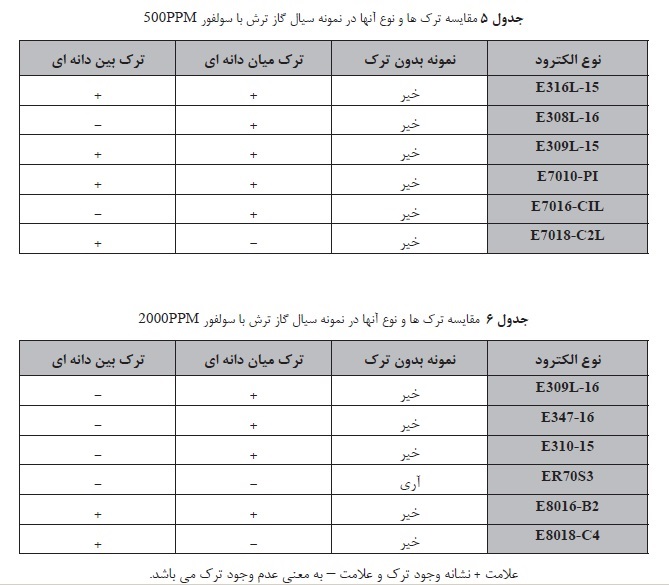
تأثیر تنش و عوامل محیطی
در نمونه های آزمایش شده با توجه به ساختار ریز دانه های آنها می توان دریافت. که با توجه به ترک های بوجود آمده سطح نمونه ها ظاهر ترد و شکننده به خود گرفته اند. و در این هنگام یک حرکت و جابجایی در تعدادی از دانه ها اتفاق افتاده است. کم کردن نوسانات مقدار حد آستانه را برای شروع ترک کم کرده و باعث افزایش میل به این گونه ترک ها می شود. مشاهده شد که با افزایش سولفور موجود در گاز ترش در نمونه های مورد آزمایش، ترک های ناشی از خوردگی تنشی بسیار محسوس تر بودند.
اما در نمونه های تحت تنش با میزان سولفور کمتر، سرعت رشد ترک به نسبت نمونه های دیگر کندتر و تابعی از زمان نیز بود. عوامل محیطی نیز از دیگر عوامل بروز ترک های ناشی از خوردگی تنشی می باشد. که با کمک تنش و ساختار آلیاژی این پدیده را تشدید می کنند. آب در نفت خام وجود دارد و حذف کامل آن مشکل است. آب به عنوان یک الکترولیت عمل نموده و باعث خوردگی می شود و همچنین اب باعث هیدرولیزه شدن مواد دیگر بویژه کلریدها میشود. بنابراین یک محیط اسیدی بوجود می آورد که با کمک تنش، عامل مخرب خواهد بود.
فولاد کربنی API 5L
موادی که در نمونه های مورد بررسی تأثیر گذار بودند، آب شور و کلریدها، سولفید هیدروژن و دی اکسید کربن و نیتروژن بوده است. ترک های ناشی از خوردگی تنشی ناشی از سولفید هیدروژن موجود در گاز. یک حالت ترکیبی از ترک میان دانه ای و بین دانه ای است. هیدرو کربن های گازی محتوی مقدار خیلی زیادی آب شور و گوگرد در شکل مرکاپتان با فرمول R-SH بودند. هر چند که این دو عامل توسط فرآیند های شیمیایی. مانند افزودن کاستیک سودا جهت حذف مرکاپتان و یا چند فازی کردن آب در دماهای مختلف جهت حذف آب شور به حداقل می رسند. اما به مقدار کم در گاز وجود دارند. که خود عاملی جهت بوجود آمدن خوردگی در مکان های مستعد می باشد.
نتیجه گیری
با توجه به مطالب و مطالعات مورد انجام که سپس بررسی شد. میتوان دریافت که عوامل عمده پیدایش ترک های ناشی از خوردگی تنشی در ساختارهای فولادی، سه عامل موادف تنش و محیط هستند. بنابراین شیوه ها و تکنیک های مهم که باعث کسب حداقل این فرآیند می گردد باید بکار روند. در این بررسی با استفاده از نمونه های استاندارد U شکل و انجام فرآیند جوشکاری بر روی این نمونه ها. با توجه به الکترودهای مختلف، تأثیر عوامل محیطی موجود در فرآیند پالایشگاه های گاز ترش بر روی نواحی جوش خطوط لوله پایش و بررسی گردیدند.
فولاد کربنی API 5L
سیالات خورنده موجود در گاز از قبیل سولفید هیدروژن، مرکاپتانها و آب های شور مخلوط شده در گازهای منتقل شونده. به کمک تنشهای موجود از عوامل مهم در ایجاد پدیده ترک های ناشی از خوردگی تنشی در ناحیه متأثر از حرارت جوش می باشد. کمترین ترک ها در استفاده از الکترودهای همسان با فلز پایه از نظر ترکیبات شیمیایی و همچنین درصد بالاتر نیکل الکترودها. نسبت به فلز پایه در ناحیه جوش نمونه های آزمایشی قابل مشاهده است.اکثر ترک های مورد ایجاد خصوصاً در نمونه های تحت آزمایش در گاز ترش با میزان سولفور بیشتر. از نوع ترک های ناشی از خوردگی تنشی میان دانه ای در ناحیه متأثر از حرارت جوش بوده اند.
از آنجاییکه گرمای جوش غالباً در منطقه جوش متمرکز می شود. چنین استنباط می گردد که کرنش و تغییر شکل مورد ایجاد. در هنگام عملیات جوشکاری می تواند سبب شکست و یا ایجاد تنش پسماند شود. این تنش های پسماند در شروع تولید ترک حائز اهمیت می باشند. استفاده از آلیاژهای کم کربن شاخه L در الکترودها، خطر حساس سازی را بوسیله کند کردن واکنش. و به باعث کسب حداقلی رسوب کاربیدهای که غنی می شوند. از کروم در راستای مرزدانه ها به حداقل می رساند.
نتیجه اینکه باعث کند شدن مسیر رشد ترک های ناشی از خوردگی تنشی در منطقه تأثیر گذار گرمایی جوش می شوند. گرمای اعمالی میزان سرد شدن در جوش دو پارامتر عمده تأثیر گذار بر روی مقاومت جوش در برابر ترک های ناشی از خوردگی تنشی و همچنین پدیده حفره دار شدن می باشد. حرارت اعمالی خیلی زیاد و میزان سرد شدن کم، سبب تفکیک عناصر آلیاژی و تشکیل مناطق خالی از کروم است. و باعث کاهش مقاومت نسبت به خوردگی موضعی می شود.
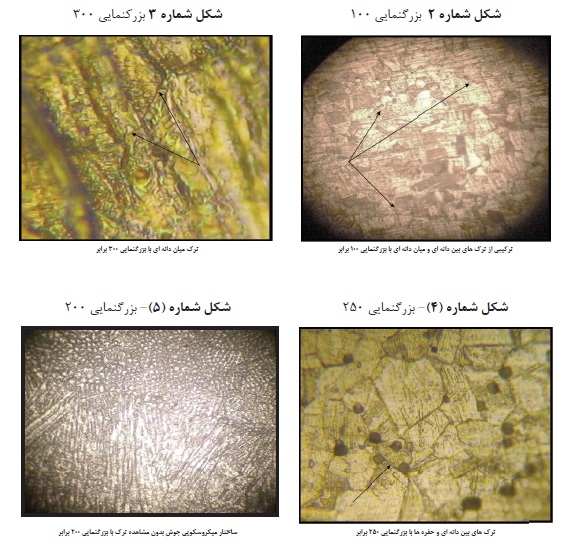
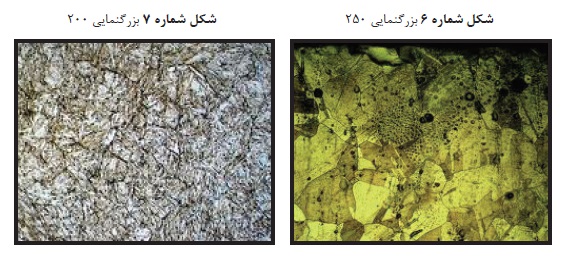
جلیل جمالی، حسین اسماعیلی مزیدی، محمد عامل کاشی پز.دانشگاه آزاد اسلامی واحد شوشتر. دانشکده مکانیک-دانشگاه آزاد اسلامی واحد علوم تحقیقات خمین.بندر عسلویه مجتمع گاز پارس جنوبی پالایشگاه چهارم
شرکت خشکه و فولاد پایتخت (( مدیریت : جواد دلاکان )) صنعتگران عزیز، افتخار داریم. که سی سال تجربه گرانبهای خویش را در زمینه عرضه انواع ورق آلیاژی. و انواع فولاد آلیاژی برای خدمت رسانی به شما هموطنان کشور عزیزمان ایران ارائه می دهیم. پیشاپیش از اینکه شرکت خشکه و فولاد پایتخت را جهت خرید خود انتخاب می نمایید سپاسگزاریم.
ارتباط با ما:
۰۹۱۲۱۲۲۴۲۲۷
۰۹۳۷۱۹۰۱۸۰۷
تلفن: ۰۲۱۶۶۸۰۰۲۵۱
فکس: ۶۶۸۰۰۵۴۶