فولاد هواپیما سازی- انواع فولاد در ساخت هواپیما
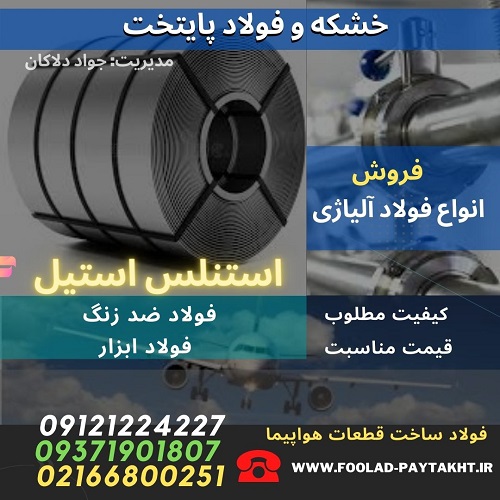
فولادهایی که در ساخت هواپیما به کار برده می شوند. باید دارای مشخصات خاصی باشند که مهمترین آنها استحکام تسلیم بالاست. هرچند امروزه صدها گرید از فولاد ساخته شده است. اما همه آنها را نمی توان در ساخت هواپیما به کار برد. از طرف دیگر از فولاد تنها در بخش های خاصی از هواپیما که نیاز است. استحکام بسیار بالایی داشته باشند.
فولاد هواپیما سازی
مانند ارابه های فرود یا محل اتصال بالها به بدنه و همچنین اسلت ها یا پیش بال ها استفاده می شود. فولادهای کم آلیاژ با کربن متوسط، فولادهای پیرسازی مارتنزیتی و همچنین استنلس استیل های PH سه گروه از فولادهایی هستند. که به دلیل استحکام تسلیم بالا به طور عمده در ساخت هواپیما از آنها استفاده میشود. در این مقاله توضیحات بیشتری در خصوص فولادهای به کار رفته در صنایع هوایی خدمت شما ارائه می گردد.
فولاد آلیاژی از آهن است که حاوی کربن و یک یا چند عنصر آلیاژی دیگر می باشد. فولاد کربنی (Carbon Steel) پرکاربردترین متریالی است که برای ساخت سازه های مهندسی مورد استفاده قرار می گیرد. از فولاد کربنی تقریباً در هر صنعتی از اتومبیل سازی گرفته تا صنایع دریایی، ریلی و زیربنایی استفاده می شود.
فولاد هواپیما سازی
مصرف جهانی فولاد در حدود 100 برابر بیشتر از آلومینیوم است که رتبه دوم در بین فلزات را دارد. در تصویر زیر می توانید میزیان مصرف فلزات مختلف مانند استیل، آلومینیوم، مواد کامپوزیت و منیزیم را در طول قرن بیستم مشاهده کنید. همانطور که دیده می شود. مصرف فولاد بیش از 90 درصد مجموع کل سایر فلزات است. هرچند از فولاد در صنایع بسیار استفاده می شود اما کاربرد آن در صنایع هوایی در مقایسه با آلومینیوم و مواد کامپوزیتی محدودتر است. استفاده از فولاد در هلیکوپترها و هواپیماها به 5 تا 8 درصد از کل وزن آنها محدود است.
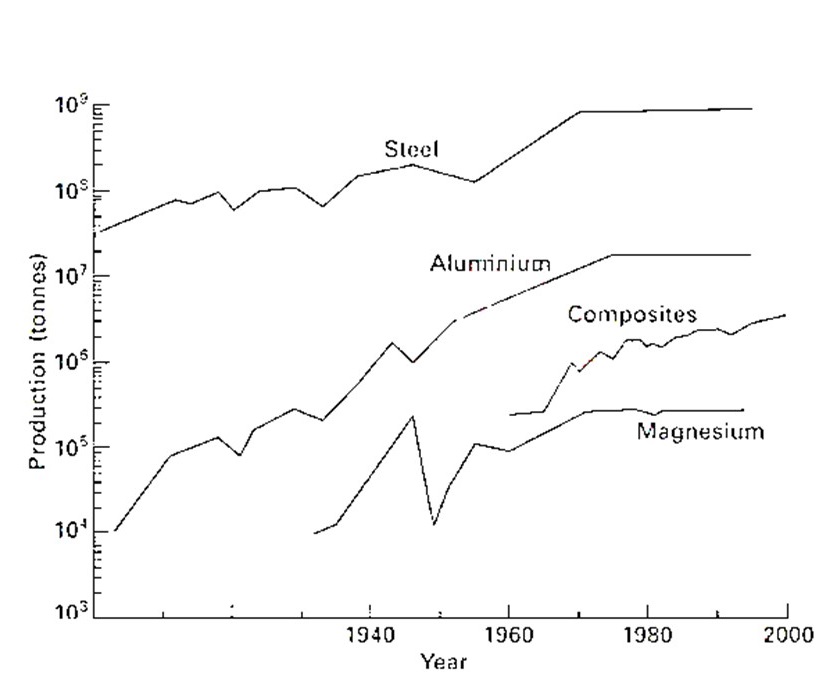
استفاده از فولاد در هواپیما معمولاً به بخش های حساس که نیاز به استحکام بسیار بالا دارد محدود می شود. به عبارت دیگر فولاد زمانی استفاده می شود که استحکام بالا بسیار مهم باشد. فولادهایی که در هواپیما استفاده میشود. استحکام تسلیمی بالاتر از 1500-2000 مگاپاسکال دارند. که از بالاترین استحکام آلومینیوم 500 – 650 مگاپاسکال یا کامپوزیت کربن – اپوکسی شبه ایزوتروپیک (Quasi-isoropic carbon – epoxy) (1000 – 750 مگاپاسکال) بسیار بالاتر است. علاوه بر استحکام بالا، فولادی که در هواپیما استفاده میشود. مدول الاستیک، سختی شکست و مقاومت خستگی بالایی دارد.
فولاد هواپیما سازی
همچنین علمکرد مکانیکی خود را در دماهای بالا (300-450 درجه سانتی گراد) نیز حفظ می کند. این ویژگی ها فولاد را به گزینه ای مناسب برای استفاده در سازه ی هواپیماهای سنگین تبدیل می کند.
هرچند از فولاد بنا به دلایلی که مهمترین آن وزن آن است در حجم های بسیار زیاد استفاده نمی شود. چگالی فولاد 7.2 گرم بر سانتیمترر مکعب است یعنی در حجم ثابت 2.5 برابر از آلومینیوم. 1.5 برابر از تیتانیوم و 3.5 برابر از کامپوزیت کربن-اپوکسی سنگین تر می باشد.
علاوه بر مشکل وزن، بیشتر فولادها نسبت به خوردگی حساس هستند. که باعث ایجاد حفره، ترک های ناشی از خوردگی و سایر اسیب ها می شود. فولادهای با استحکام بالا (High-strength) نیز مستعد تردی هیدروژنی (Hydrogen Embrittlement) ناشی از جذب هیدروژن هستند که نقطه ضعفی برای آنها به شمار می آید. غلظت بسیار کم هیدروژن حتی به اندازه 0.0001 درصد در فولاد می تواند باعث ترک هایی شود. که منجر به شکست در سطح تنش هایی کمتر از سحط استحکام تسلیم می شود.
قسمت هایی از سازه هواپیما که در آن از فولاد مقاومت بالا استفاده می شود. شامل چرخ های هواپیما، اتصالات بال، شاه تیرهای موتور و اسلت یا پیش بالاهاست. در شکل زیر می توانید از قسمت ها را ملاحظه کنید. بیشترین کاربرد فولاد نیز در ارابه های فرود ( Gear Landing) است. استفاده از فولاد در این قسمت به دلیل نیاز به سختی بالا، استحکام و مقاومت به خستگی زیاد است. چرا که در زمان فرود و تیک آف هواپیما نیروی بسیاری زیادی به این قسمت وارد می شود. به دلیل استحکام زیاد فولاد این قسمت از هواپیما می تواند نسبتاً کوچک ساخته شود. به گونه ای که به راحتی در قسمت زیر شکم هواپیما فضای بسیار کمی را اشغال کند. از فولاد همچنین در ریشه اتصال بال به بدنه و اسلت بال ها نیز استفاده می شود.
فولاد هواپیما سازی
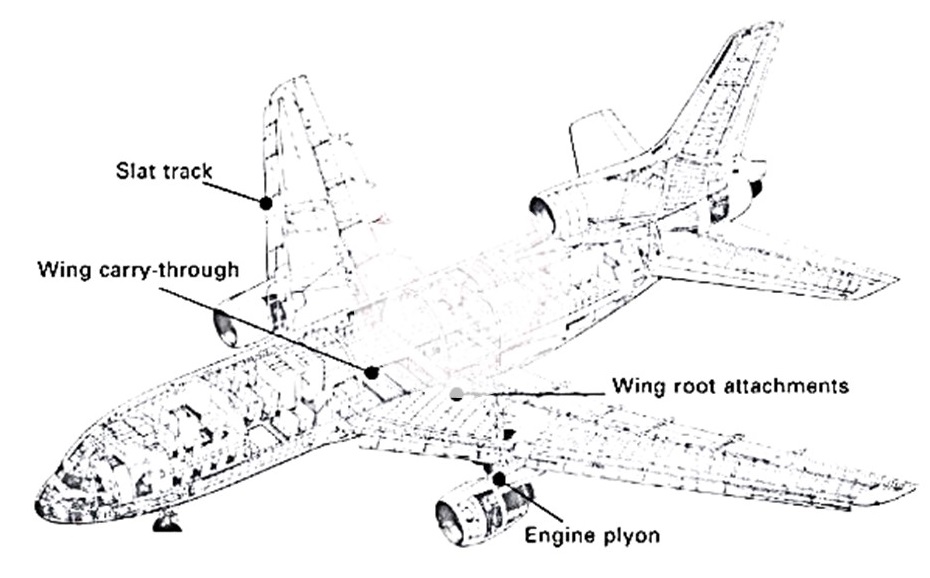
گرید های فولاد
آهن با کربن و وسایر عناصر ترکیب شده و پس از عملیات فورجینگ و حرارتی فولاد مقاومت بالا را می سازد. آهن خالص فلزی نرم است که استحکام تسلیمی کمتر از 100 مگاپاسکال دارد. اما به کمک ترکیب با فولاد و برخی عناصر آلیاژی و همچنین انجام عملیات های حرارتی استحکام آن افزایش داده می شود. به کمک ترکیب عناصر و همچنین فرآیندهای ترمودینامیکی می توان فولادهایی ساخت که استحکام تسلیم آن از 200 تا بالای 2000 مگاپاسکال متغیر است. برخی ویژگی های مهم دیگر فولاد از قبیل سختی، مقاومت به خستگی. و مقاومت خزشی نیز به وسیله ی عملیات ترمودینامیکی و آلیاژی قابل کنترل است.
امروزه بیش از صدها گرید مختلف فولاد وجود دارد. اگرچه تنها تعداد بسیار کمی از آنها دارای مقاومت و سختی بالا در حدی است که بتوان در صنعت هواپیماسازی از آنها استفاده کرد. فولادهای حاوی کمتر از 1.5 درصد کربن (همراه با سایر عناصر آلیاژی) هستند. و اغلب بر اساس مقدار کربن و عناصر آلیاژی که در خود دارند دسته بندی می شوند. برخی از مهمترین گروه های فولاد عبارتند از:
فولاد معمولی یا فولاد نرم
فولادهای معمولی که به عنوان فولادهای کم کربن نیز شناخته می شوند. کمتر از 2 درصد کرن در خود دارند و عموماً به وسیلۀ سردکاری سخت می شوند. فولاد معمولی استحکام تسلیم متوسط در حد 200 تا 300 مگاپاسکال دارد و به دلیل نرم بودن در صنایع هوایی کاربردی ندارد.
فولادهای کم آلیاژ مقاومت بالا
فلزهای کم آلیاژ مقاومت بالا (HSLA) فولادهایی هستند. که مقدار کمی کربن (کمتر از 0.2 درصد) مانند فولاد معمولی دارند. و مقدار کمی نیز عناصر آلیاژی مانند مس، نیکل، نیوبیوم، وانادیوم، کروم، مولیبدینوم و زیرکونیم در آنها استفاده می شود. فولادهای HSLA به عنوان فولادهای میکروآلیاژی شناخته می شوند. چرا که در مقایسه با سایر انواع فولادها مقدار عناصر آلیاژی آن بسیار کمتر است. استحکام تسلیم فولادهای HSLA بین 250 تا 600 مگاپاسکال است و در اتومبیل سازی، ساخت کامیون و پل سازی کاربرد دارد. استفاده از HSLA در صنعت هواپیمایی نیز کم است چرا که استحکام و مقاومت کمی در برابر خوردگی دارد.
فولاد هواپیما سازی
فولاد کربن متوسط
فولادهای کربن متوسط بین 0.25 تا 0.5 درصد کربن دارند و به وسیلۀ فرایندهای ترمومکانیکی به سختی بین 300 تا 1000 مگاپاسکال می رسند. این گروه از فولادها برای کاربردهای سازه ای بسیار مورد استفاده قرار می گیرند. در موتور اتومبیل ها، سازه های ساختمان ها و پل ها، کشتی ها، وگن های قطار و سازه های دور از دریا استفاده می شود. فولادهای کم کربن در صنایع هوایی کاربرد کمی دارد.
فولادهای کم آلیاژ کربن متوسط
فلزهای کم آلیاژ کم کربن بین 0.25 تا 0.5 درصد کربن دارند اما مقدار عناصر آلیاژی آن بیشتر است. که موجب افزایش سختی و و مقاومت آن در دمای بالاست. در ساختار این فولادها عناصری مانند نیکل، کروم، مولیبدنوم، وانادیوم و کبالت وجود دارد. نمونه های آلیاژ بالای این فولادها در ساخت فولاد ابزار استفاده می شود. ابزاری مانند مته، تیغه و قطعات ماشین ها که به سختی و مقاومت سایشی بالای در دماهای بالا نیاز دارند. سطح استحکام این فولادها به 2000 مگاپاسکال نیز می رسد. از این فولادها در ساخت هواپیما و به طور عمده در قسمت های ارابه فرود (Undercarriage) استفاده می شود.
فولادهای پیرسازی مارتنزیتی
فولادهای پیرسازی مارتنزیتی (Mareging steels) حاوی مقدار بسیار بالایی عنصر آلیاژی و مقدار بسیار کمی (کمتر از 0.03 درصد) کربن هستند. در کنار عملیات حرارتی که شامل سخت پیرسازی است. این دسته از فولادهای ترکیبی از استحکام بسیار بالا، سختی شکست و چکش خواری را دارا هستند. استحکام فولادهای پیرسازی مارتنزیتی در زنج 1500 تا 2300 مگاپاسکال قرار دارد و آنها را در زمره قوی ترین مواد فلزی قرار می دهد. از این گروه از فولاد در اجزایی از هواپیما که بارگذاری سنگین روی آن انجام می شود استفاده می گردد.
فولاد ضد زنگ
فولادهای ضد زنگ یا استنلس استیل ها موادی هستند که حاوی 0.08 تا 0.25 درصد کربن. و مقدار بالایی کروم (12 تا 26 درصد) می باشند. برخی مواقع از نیکل ( تا 22 درصد) نیز در ساخت استنلس استیل ها استفاده میشود. گریدهای مختلفی از استنلس استیل ها با مشخصات مکانیکی گوناگون وجود دارد . که استحکام تسلیمی بین 200 تا 2000 مگاپاسکال را می توانند داشته باشند. استیل های PH یا سخت کاری رسوبی به کاربردهای مرتبط با هوافضا بیشتر مورد استفاده قرار می گیرند. به این دلیل این کلاس از استیل در کنار مقاومت به خوردگی استحکام بالایی را نیز دارا هستند.
از میان تمام فولادهایی که ساخته شده و موجود هستند. فولادهای کم آلیاژ با کربن متوسط، فولادهای پیرسازی مارتنزیتی و استیل های PH بیشترین کاربرد را در ساخت هواپیما دارند.
در جدول زیر می توانید مشخصات فولادهایی که به صورت عمده در هواپیماسازی استفاده می شوند را مشاهده نمایید
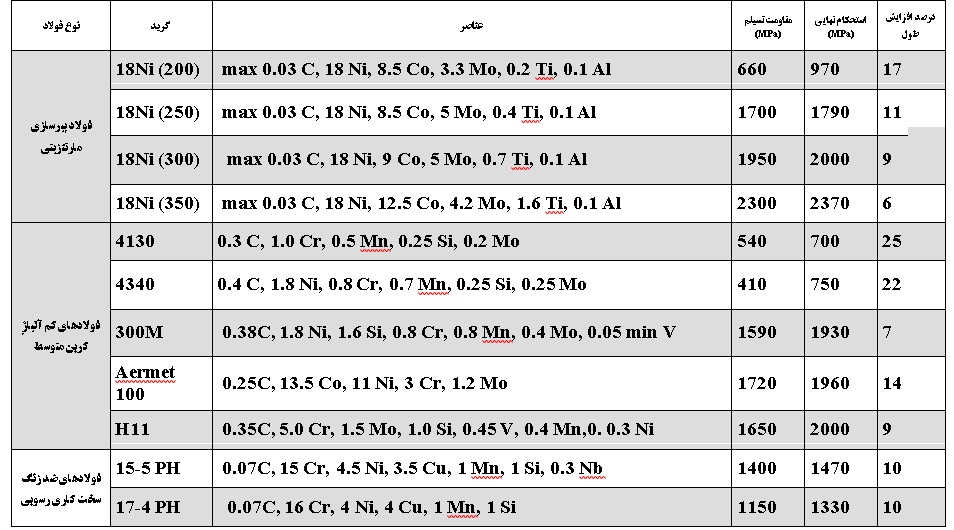
شرکت خشکه و فولاد پایتخت (( مدیریت : جواد دلاکان )) صنعتگران عزیز، افتخار داریم. که سی سال تجربه گرانبهای خویش را در زمینه عرضه انواع ورق آلیاژی. و انواع فولاد آلیاژی برای خدمت رسانی به شما هموطنان کشور عزیزمان ایران ارائه می دهیم. پیشاپیش از اینکه شرکت خشکه و فولاد پایتخت را جهت خرید خود انتخاب می نمایید سپاسگزاریم.ارتباط با ما:
۰۹۱۲۱۲۲۴۲۲۷
۰۹۳۷۱۹۰۱۸۰۷
تلفن: ۰۲۱۶۶۸۰۰۲۵۱
فکس: ۶۶۸۰۰۵۴۶