اکستروژن – برون ريزي
اکستروژن يا برون ريزي يکي از روش هاي حجمي، براي تغيير شکل مواد. به منظور کاهش ضخامت يا سطح مقطع آنهاست که در نتيجه آن، قطعاتي با سطح مقطع صاف و عمودي توليد مي شوند.
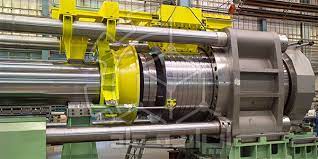
جهت انجام فرآيند اکستروژن، ماده اوليه مورد نظر، به درون قالب اکستروژن که سطح مقطع مورد نظر روي آن ايجاد مي شود و پرس مي شود. و در نتيجه، قطعه اکسترود مي شود و با سطح مقطع قالب، توليد مي شود. دو مزيت اين فرآيند، نسبت به ديگر روش هاي شکل دهي. قابليت بالا در توليد قطعاتي با سطح مقطع پيچيده و همچنين شکل دهي مواد ترد و شکننده است،
زيرا ماده در اين روش، تنها تحت فشار و تنش برشي قرار مي گيرد. اين روش همچنين قطعاتي، با سطح مقطع بسيار با کيفيت و صاف ايجاد مي کند و باعث استحکام بيشتر مواد مي شود. اکستروژن مي تواند پيوسته (توليد قطعات با طول زياد) يا نيمه پيوسته (توليد چند تکه اي) باشد. فرآيند اکستروژن مي تواند با مواد اوليه سرد يا گرم انجام شود. انواع موادي که اکستروژن روي آنها انجام مي شود عبارتند از: فلزات، پليمرها، سراميک ها و مواد غذايي و …
تاريخچه
در سال 1797، Joseph Bramah اولين فرآيند اکستروژن براي توليد لوله از مواد نرم را انجام داد. او ابتدا ماده اوليه فلزي را پيش گرم کرد و آن را به وسيله يک پيستون دستي متحرک، به داخل قالب حرکت داد. در سال 1820، Thomas Burr همين فرآيند را به وسيله يک پرس هيدروليک انجام داد. در سال 1844، Alexander Dick، فرآيند اکستروژن را براي آلياژهاي مسي و برنجي نيز گسترش داد.
دستگاه پرس اکستروژن
در اين دستگاه از پيستون قوي جهت اعمال بار يکنواخت بر قطعه مورد نظر. و با فشار و پرس آن در بدنه دستگاه به کار مي رود. از آنجايي که اصطکاک ميان بدنه دستگاه و قطعه زياد است. درجه حرارت نيز زياد مي شود؛ بنابراين لازم مي شود که بدنه دستگاه هرچند بار خنک کاري شود. جهت خنک کاري از آب صابون يا روغن استفاده مي شود. جنس بدنه اين دستگاه بايد مقاوم باشد تا بتواند تنش هاي وارد بر آن را تحمل کند. حنس بدنه معمولاً از تنگستن کربونايد است.
فرآيند اکستروژن
فرآيند اکستروژن، با گرم کردن مواد اوليه (در اکستروژن گرم) شروع مي شود. سپس داخل مخزن دستگاه پرس قرارمي گيرد. (مواد اوليه فلزي، به صورت بيلت هاي استوانه اي ريخته گري مي شود و داخل مخزن دستگاه پرس قرار مي گيرند). سپس يک قطعه حائل بين بيلت و پيستون قرار مي گيرد و بيلت توسط پيستون به داخل قالب، فشرده مي شود. سپس محصول اکسترود مي شود از سمت ديگر کشش پيدا مي کند تا صاف شود. براي بهبود خواص محصول بايد روي آن فرآيندهاي گرم کاري و سرد کاري انجام شود.
عيوب اکستروژن
- ممکن است روي سطح محصول، ترک هاي سطحي اتفاق بيفتد. دليل ايجاد اين ترک ها مي تواند دماي فرايند اکستروژن، اصطکاک، يا زياد بودن سرعت پيستون باشد. ترک هاي سطحي مي توانند در دماهاي پايين تر هم ايجاد شوند و اين اتفاق زماني رخ مي دهد که محصول اکستروژن به قالب بچسبد.
- الگوهاي جرياني، اکسيدها و آلودگي هاي سطحي را به سمت مرکز محصول اکستروژن هدايت مي کنند و باعث کاهش استحکام محصول مي شود. اين عيب به دليل وجود اصطکاک و فرآيندهاي سردکاري روي لاي? خارجي بيلت، اتفاق مي افتد.
- ترک هاي داخلي که به دليل وجود تنش هاي داخلي، هنگام عبور بيلت از قالب. و در اثر نيروي فشاري پيستون در محصول نهايي ايجاد مي شود. و باعث کاهش استحکام نهايي محصول مي شود.
- خطوط سطحي، اين خطوط روي محصولات اکستروژن معلوم است. ايجاد اين عيب به ميزان زيادي به کيفيت قالب اکستروژن و نحوه ساخت آن بستگي دارد. دليل ديگري که مي تواند باعث وجود اين عيب در محصولات اکستروژن شود، چسبيدن محصول خروجي به ديواره قالب است.
تجهيزات و انواع روش هاي اکستروژن
تجهيزات مختلفي جهت انجام يک فرآيند اکستِروژن وجود دارد که 4 ويژگي زير، باعث تمايز آن ها مي شوند:
- جهت حرکت محصول اکستروژن نسبت به جهت حرکت پيستون، اگر قالب ساکن باشد. و پيستون حرکت کند، فرايند «اکستروژن مستقيم» و اگر پيستون به صورت ساکن قرار گيرد. و قالب درون دستگاه حرکت کند، «اکستروژن مستقيم» بيان مي شود.
- نوع پرس اکستِروژن که مي تواند عمودي يا افقي باشد.
- از نوع سيستم محرک که مي تواند هيدروليک يا مکانيکي باشد.
- نوع بارگذارري آن که مي تواند متغير يا هيدرواستاتيک باشد.
يک مت? تک يا دوبل که به وسيله يک پيستون يا موتور الکتريکي تغذيه مي شود. به وسيله يک فشار هيدروليک يا يک فرآيند مشابه، رانده مي شود تا محصولات اکستروژن از ماده اوليه، حاصل شود.
ايجاد حفره هاي داخلي
روش هاي مختلفي براي ايجاد حفره هاي داخلي در يک فرآيند اکستروژن وجود دارد. يک راه، استفاده از يک بيلت ميان تهي است. که درون بيلت اوليه، حفره با شکل مورد نظر از ابتدا با يکي از روش هاي ساخت، ايجاد مي شود. به منظور ايجاد حفره ها، با دقت ابعادي بالاتر از ماندرل استفاده مي شود. ماندرل ها بر دو نوع هستند:
1- ماندرل شناور-(ماندرل نوع فرانسوي): داخل قطعه حائل بين بيلت و قالب به صورت آزادانه قرار مي گيرد. و هنگام انجام فرآيند، خود را درون قالب، جا مي اندازد و به اين ترتيب، حفره مورد نظر درون محصول اکستروژن ايجاد مي شود.
2- ماندرل ثابت- (ماندرل نوع آلماني): همانند قالب توليد مي شود و قبل از قالب قرار مي گيرد. و در نتيج? عبور از آن، حفره داخلي در مواد ايجاد مي شود و سپس با عبور از قالب، محصول نهايي اکستروژن توليد مي شود.
اکستروژن مستقيم
اکستروژن مستقيم، رايج ترين نوع اکستروژن است که در آن جهت حرکت پيستون و محصول اکستروژن يکسان است. در حقيقت در اين روش، قالب ثابت است و پيستون، بيلت را به درون قالب حرکت مي دهد. در اين روش، بيلت داخل يک محفظ? مورد محافظت قرار مي گيرد. سپس بيلت به وسيله فشار پيستون، به داخل قالب رانده مي شود. در اين مرحله، يک قطعه حائل بين پيستون و بيلت قرار مي گيرد تا آنها را جدا از هم نگه دارد. در نتيجه اين فرآيند، محصول اکستروژن از سمت ديگر دستگاه، در جهت يکسان با جهت حرکت پيستون، خارج مي شود.
عيب اصلي اين روش نسبت به روش غيرمستقيم اين است. که در اين روش، به دليل وجود نيروهاي اصطکاکي در اثر حرکت بيلت در طول مخزن، نيروي بيشتري جهت شروع فرايند اکستروژن لازم است. و با حرکت بيشتر بيلت، اين نيرو رفته رفته کاهش مي يابد. در انتهاي بيلت نيز نيرو به شدت افزايش مي يابد. زيرا بيلت در اين قسمت باريک است و ماده بايد به صورت شعاعي از قالب خارج شود. به همين دليل انتهاي بيلت بدون استفاده مي ماند و در انتهاي فرآيند بايد بريده شود.
اکستروژن غير مستقيم
در اکستروژن غير مستقيم، جهت حرکت پيستون و محصول اکستروژن، مخالف يکديگر هستند. در اين روش، بيلت و محفظه اي که بيلت داخل آن قرار دارد. با يکديگر به سمت قالب که ثابت است حرکت مي کنند. به دليل اينکه در اين روش بيلت و محفظه با يکديگر حرکت مي کنند. نيروي اصطکاکي که بين آنها کاهش مي يابد. مزاياي اين روش عبارتند از:
- 30% -25 کاهش اثرات نيروي اصطکاک که به همين دليل در اين روش، مي توان بيلت هاي با طول بيشتري را اکسترود کرد.
- به دليل کاهش حرارت ناشي از اصطکاک، احتمال ايجاد و رشد ترک و محصول اکستروژن، به حداقل مي رسد.
- استفاده از اين روش باعث کاهش عيوب ناشي از اکستروژن در محصول اکستروژن مي شود.
معايب اين روش عبارتند از:
- ناخالصي ها و عيوب سطحي بيلت، بر روي سطح محصول اکستروژن نيز تأثير مي گذارد.
- کاربرد محدودتري نسبت به اکستروژن مستقيم دارد. زيرا محفظه اي که قالب در آن قرار مي گيرد، باعث محدوديت در ابعاد سطح مقطع محصول مي شود.
اکستروژن هيدرواستاتيک
يکي از روش هاي متداول شکل دهي شديد فلزات، اکستروژن هيدرواستاتيک (Hydrostatic Extrusion) مي باشد.
اين روش نوين جزو زيرشاخه هاي اکستروژن مي باشد که به سه صورت سرد، گرم و داغ انجام مي پذيرد. اولين استفاده کاربردي و صنعتي اکستروژن هيدرواستاتيک از سال 1893 ميلادي شروع مي شود. با اين وجود، پيشرفت اين روش به خصوص در توليد مواد نانو ساختار در سال هاي اخير انجام شد. روش انجام اين فرآيند بسيار ساده مي باشد. بدين صورت که يک بيلت (به صورت استوانه اي شکل) اوليه در داخل محفظه اکستروژن قرار مي گيرد.
سپس توسط پيستون پرس (Ram) مانند، فشار به يک سيال (Fluid) منتقل مي گردد. و در نهايت فشار يکنواخت سيال روي بيلت اوليه، موجب تغيير شکل و اکستروژن ماده مي گردد. به خاطر ايجاد تغيير شکل يکنواخت و همچنين امکان ايجاد نرخ کرنش هاي بالا (104 بر ثانيه) ضريب اصطکاک بين بيلت و قالب کم در نظر مي گيرند. همچنين با انتخاب زاويه قالب کوچک نيز مي توان به تغيير شکل همگن و يکنواخت دست يافت. با استفاده از اين روش مي توان مواد نانو ساختار با اشکال مختلف با سطح مقطع هاي پيچيده توليد کرد. با توجه به پارامترهاي مختلف فرايند در هر مرحله از برون ريزي، کرنشهاي بالا (در حدود هشت) را مي توان ايجاد کرد.
البته لازم است ذکر شود. که براي رسيدن به مواد با اندازه نانو اين فرايند بايد در چند مرحله انجام پذيرد. همچنين بايد در نظر داشت که نرخ کرنش بالا نبايد بيش از حد زياد باشد. زيرا باعث فشار بيش از حد به بدنه قالب مي گردد. در اين روش به دليل استفاده از فشار هيدرواستاتيک اکسترود شدن مواد به صورت يکنواخت انجام مي گيرد. با مقايسه ديگر روش هاي تغيير شکل شديد مانند پرس با قالب زاويه دار (ECAP)، پيچش با فشار زياد (HPT). و اکستروژن دوره اي و تکنيک فشار (CEC) مي توان با کرنش کمتر به اندازه دانه يکسان دست يافت.
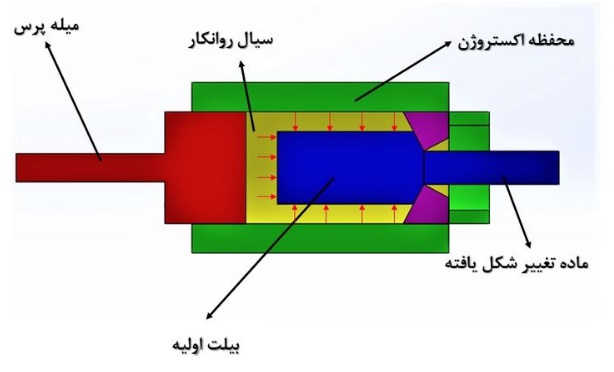
مزايا و محدوديت هاي اکستروژن هيدرواستاتيک
اکستروژن هيدرواستاتيک در مقايسه به اکستروژن سنتي داراي مزايا و معايب مختلف مي باشد. از جمله مزاياي اين روش مي توان به سه مورد اشاره کرد. الف) فشار موجود در اين فرآيند به طول بيلت مورد آزمايش بستگي دارد. زيرا اصطکاک بين بيلت و محفظه اکستروژن از بين مي رود. ب) فشار کل موجود بين بيلت و محفظه و بيلت با قالب به خاطر عدم وجود اصطکاک. ناشي از بيلت با محفظه بسيار کم مي باشد. ج) به خاطر اعمال تنش هيدرواستاتيک خميدگي ماده اکسترود شد وجود نداشته و ماده با ساختار همگن توليد مي شود.
با اين وجود اين فرآيند داراي محدوديت هايي نيز مي باشد. که از جمله آن ها عبارتند از: الف) مشکل شدن طراحي ايمن محفظه به خاطر استفاده مداوم از فشارهاي بالا. ب) بارگذاري پيچيده به خاطر وجود سيال و فشار بالا و در نهايت ج) کاهش راندمان فرآيند با افزايش فشار وارد بر سيال. همچنين به خاطر روغن کاري مداوم و سيکل وار در فرآيند اکستروژن رفتار چسبش – لغزش (Slip-Stick) مشاهده مي شود. اين پديده باعث مي شود تا فشار لازم ثابت نبوده و از فشار در حالت ثابت (فشار بهينه) منحرف گردد. پديده چسبش – لغزش همچنين باعث تغييرات در قطر بيلت و عدم ثبات در فرايند مي شود.
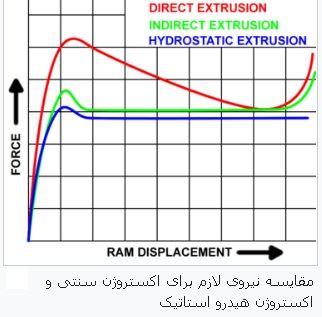
پارامترهاي اکستروژن هيدرواستاتيک
پارامترهاي مختلفي بر روي فرايند تأثيرگذار مي باشند. از جمله اين پارامترها مي توان به فشار اکستروژن (Pex) زاويه قالب (die angle)، نرخ اکستروژن (ratio of extrusion) و سيال مورد استفاده اشاره کرد. کنترل هر کدام يک از اين پارامترها منجر به تغييرات محسوس در فرايند اکستروژن هيدرواستاتيک مي گردد.
فشار اکستروژن
مي توان با اطمينان گفت يکي از اساسي ترين متغيرهاي فرايند هيدرواستاتيک تغيين فشار اکستروژن مي باشد. به عبارت ديگر، هرگونه اشتباه در تعيين فشار اکستروژن باعث به وجود آمدن اختلال در امر اکستروژن خواهد شد. علاوه بر اين، فشار اکستروژن خود تابعي از چهار پارامتر ديگر مي باشد. الف) زاويه قالب، ب) نرخ اکستروژن، ج) ضريب اصطکاک و د) استحکام تسليم ماده بيلت. با افزايش ضريب اصطکاک کار لازم براي غلبه بر نيروي اصطکاک بيشترمي شود. و به تبع آن فشار لازم براي تغيير شکل بيلت افزايش مي يابد. همچنين مي توان گفت که با افزايش استحکام تسليم، فشار بيشتري براي تغيير شکل ماده نياز مي باشد. در نهايت ميتوان اين گونه اظهار داشت که تعيين درست فشار اکستروژن کمک شاياني به بهبود عملکرد اکستروژن هيدرواستاتيک مي نمايد.
زاويه قالب
پارامتر ديگري که نقش مهمي در بالا بردن راندمان کاري دارد. زاويه قالب مورد استفاده در فرآيند اکستروژن هيدرواستاتيک مي باشد. به طور کلي سه نوع کار در فرآيند اکستروژن وجود دارد. الف) کار تغيير شکل همگن يا کمترين کار لازم براي تغيير شکل بيلت به شکل نهائي. ب) کار مازاد (Redundant Work) که در اثر پديده برش معکوس در ناحيه تغيير شکل ايجاد مي شود.
و ج) کار نيروي اصطکاک که در اثر اصطکاک بين ديواره قالب و بيلت ايجاد مي شود. کار نيروي اصطکاک با زاويه قالب در تناسب مي باشد. به عبارت ساده تر، هر چه زاويه قالب افزايش يابد، سطح تماس بين بيلت و ديواره قالب کمتر مي شود. و نيروي اصطکاک کمتر مي شود. اين پديده باعث کاهش فشار لازم براي تغيير شکل مي گردد. زيرا کار لازم براي غلبه بر اصطکاک توسط فشار اکستروژن تأمين مي گردد. به طور خلاصه مي توان بيان کرد که زاويه قالب همواره بايد مقدار بهينه اي داشته باشد تا راندمان کاري افزايش يابد.
نرخ اکستروژن
يکي ديگر از پارامترهاي تأثير گذار در راندمان فرايند اکستروژن هيدرواستاتيک. نرخ اکستروژن يا به عبارت ساده تر ميزان کاهش سطح مقطع (Area Reduction of Surface) مي باشد. در يک زاويه قالب ثابت، افزايش ميزان نرخ اکستروژن منجر به افزايش سطح تماس بين بيلت و ديواره قالب مي شود. و در نتيجه فشار زيادي براي غلبه بر کار سختي ناشي از کرنش زياد نياز مي باشد.
روانکاري قالب و بيلت
روانکاري مناسب بين سطوح بيلت و قالب در فرآيند اکستروژن منجر به کاهش فشار اکستروژن مي گردد. سايل روانکار بايد خواص ويژه اي داشته باشد. تا بهترين کارايي را در فرايند اکستروژن داشته باشد. از جمله پارامترهاي مهم در انتخاب روانکار مناسب، ويسکوزيته و ضخامت فيلم روانکار مي باشد. ضخامت فيلم روانکار تأثير قابل توجهي بر روي اصطکاک بين بيلت و ديواره قالب مي گذارد. به عبارت ديگر، با افزايش ضخامت روانکار، تماس بين بيلت و ديواره قالب کاهش مي يابد و کار نيروي اصطکاک مورد کاهش است.
و در نهايت فشار لازم براي تغيير شکل نيز کاهش قابل توجه در صافي سطح پاياني مواد دارد. به طور خلاصه تر مي توان گفت که استفاده از روانکار با ضخامت ضخيم منجر به صافي سطح پايين مي گردد. از طرف ديگر، به دست آوردن سطوح با صافي سطح بالا را مي توان با استفاده از روانکار با ضخامت پايين به دست آورد. ويسکوزيته نيز عاملي ديگر در انتخاب روانکار مي باشد. با افزايش ويسکوزيته شرايط تغيير شکل بدتر مي گردد و منجر به ايجاد ترک در بيلت و ماده نهايي مي گردد.
اکستروژن مواد غذايي
اکستروژن مواد غذايي که امروژه به منظور تهيه فراورده هاي پاستا و ساير فراورده هاي که شکل پذير مي گردد. غلات آماده مصرف، اسنک، غذاي حيوانات خانگي، فراورده هاي قنادي، نشاسته اصلاح شده مخصوص سوپ. غذاي کودک، غذاي آماده و پايه اي براي توليد نوشيدني مورد مصرف فراوان قرار مي گيرد. به يکي از فرايندهاي مهم تبديل ميشود. اين فرايند نوعي پخت محسوب مي شود. که مي توان از آن در توليد فراورده هاي داراي پُف و تُرد استفاده کرد. اين فرايند، به صورت مداوم است و در آن دماي بالا و زمان کوتاه اعمال ي شود. و در سالهاي اخير در سطح جهاني به يکي از مشهورترين فرايندهاي اقتصادي براي فرموله کردن محصولات بر پايه غلات تبديل مي شود.
اکستروژن را مي توان به عنوان فرايندي که در آن موادي مثل نشاسته ذوب شده. با فشار از خروجي (داي) به منظور ايجاد شکل خاص عبور مي يابد. تعريف کرد. در حين فرايند اکستِروژن، انرژي حرارتي حاصل، همراه با انرژي مکانيکي (برشي) تغييرات فيزيکو شيميايي سريعي در ماده اوليه ايجاد مي کند. يکي از مهم ترين ويژگي هاي فرايند اکستروژن ايجاد پف به فراورده است که بافت ماده غذايي را تحت تأثير قرار مي دهد. فناوري اکستروژن به عنوان يک فرايند توليدي کارا، نقش مهمي در صنايع غذايي بر عهده دارد.
اين فرايند متشکل از عمليات جابجايي، اختلاط برش، حرارت و تبريد. شکل دادن، خروج مواد فرار و رطوبت، ايجاد طعم، انکپسولاسيون و استريليزاسيون مي باشد. اين فرايند مي تواند در دماي پايين (مثل توليد فراورده هاي خميري) يا در دماهاي بالا (مثل توليد اسنک) اجرا شود. در بعضي از سيستم ها، به دليل وجود فشار، آب در حالت مايع فوق داغ است. که اين موضوع کنترل عمل شکل پذيري را تسهيل مي کند. و نيروي برشي را افزايش مي دهد. اين فشار مي تواند بين 25 تا بيش از 200 بار متغير باشد.
شرکت خشکه و فولاد پايتخت (( مديريت : جواد دلاکان )) صنعتگران عزيز، افتخار داريم. که سي سال تجربه گرانبهاي خويش را در زمينه عرضه انواع ورق آلياژي. و انواع فولاد آلياژي براي خدمت رساني به شما هموطنان کشور عزيزمان ايران ارائه مي دهيم. پيشاپيش از اينکه شرکت خشکه و فولاد پايتخت را جهت خريد خود انتخاب مي نماييد سپاسگزاريم.
ارتباط با ما:
09121224227
09371901807
تلفن: 02166800251
فکس: 66800546