لوله مانیسمان A333-فولاد A333، نوعی از لوله های فولادی است و لوله فولادی کربنی و آلیاژی برای استفاده در دماهای پایین را پوشش می دهد. درجات مختلفی از فولاد ضد زنگ وجود دارد.
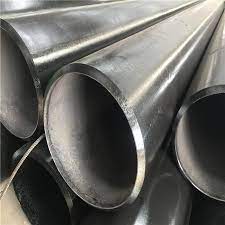
برخی از اندازه های محصول ممکن است در این مشخصات موجود نباشند زیرا ضخامت دیواره بیشتر تأثیری منفی بر خواص ضربه در دمای پایین دارد.
این مشخصات، جداره لوله را تقریباً بطور انحصاری و در کل پوشش می دهد. درجات مختلفی از فولاد ضد زنگ وجود دارد. برخی از اندازه های محصول ممکن است در این مشخصات موجود نباشند. چون ضخامت دیواره بیشتر تأثیری منفی بر خواص ضربه در دمای پایین دارد. لوله مانیسمان A333 با 9 گرید متفاوت با اعداد 1،3،4،6،7،9،10،11 بیان می شود.
طیف وسیعی از محصولات تولیدی شامل لوله های فولادی کربنی ASTM A333 و لوله های فولادی کربنی ASTM A333 گرید 3 و همچنین محصولات بیشتری است. کلیه محصولات با استفاده از آخرین فناوری که مطابق با مشخصات صنعت است تولید می گردد.
لوله های بدون درز ASTM A333 گرید 3 از جنس فولاد کربنی با مقاومت در برابر خوردگی و اکسیداسیون در دماهای بالا هستند.
همچنین لوله های کربن A333 در اندازه ها و شکل های مختلف تولید می کنند. و از فولادهای با کیفیت و مرغوب برای تهیه این لوله های کربن A333 به طور گسترده در صنایع پتروشیمی، گاز طبیعی. نفت و گاز و ساخت و ساز و سایر صنایع استفاده می شود، بهره می برند.
ASTM A333 لوله فولادی کربن و آلیاژی بدون درز و جوش وجود دارد. که برای استفاده در دماهای پایین مورد استفاده قرار می گیرند. شامل چندین درجه از فولاد فریتیک است. تحت این مشخصات، اندازه های خاص محصول ممکن است در دسترس نباشد. زیرا ضخامت دیواره های بزرگتر می توانند بر عملکرد ضربه ای دما تأثیر منفی بگذارند.
لوله های فولادی کربنی ASTM A333 گرید 3/6
- محدوده اندازه: از 1/2 اینچ تا 36 اینچ
- ضخامت: رده 40،60،80
- برنامه های کاربردی: پلایشگاه های نفت، پتروشیمی، تولید برق (هسته ای-حرارتی)، فولاد، تجهیزات بویلر، مخازن تحت فشار و اهداف مهندسی عمومی
- نوع: بدون درز /ERW/ جوش داده شده/CDW
- فرم: لوله/گرد/قوطی های مربعی/قوطی های مستطیلی/کویل/لوله های هیدرولیک
- پوشش بیروننی: رنگ سیاه، روغن ضد خوردگی، روکش گالوانیزه، هر پوششی مطابق با نیاز مشتری
تست مکانیکی
آزمون تست کششی عرضی یا طولی، تست کشش، تست سختی. یا تست خمیدگی برای بررسی رفتار مواد مورد حرارت دهی در نوعی کوره استفاده می شود.آزمایشات باید بر روی 5 درصد از هر مقادیر لوله انجام شود. برای قطعات کوچک، حداقل یک لوله باید آزمایش شود. برای حرارت موادی که با فرآیند مستمر مورد استفاده قرار می گیرد. آزمایشات باید بر تعداد کافی لوله انجام شود تا 5% از قطعه را تشکل دهد. اما در هر صورت کمتر از 2 لوله باشد.
آزمون ضربه ای هیدرواستاتیک یک آزمون ضربه محکم و ناگهانی است. که شامل شکست سه نمونه است و باید از هر گرمای اعمالی. در یک بار حرارتی بر روی نمونه های گرفته شده از لوله به انجام رسد.
کاربردهای متداول لوله بدون درز فولاد کربن ASTM A333
لوله بدون درز ASTM A333 از فولاد کربن نه تنها برای مهمترین کاربردهای مهندسی بلکه برای کاربردهای خاص در بخش خودرو نیز استفاده می شود. لوله کشی ASTM A333 برای کابردهای مکانیکی و فشار بالا و همچنین برای استفاده عمومی در خطوط بخار، آب، گاز طبیعی و هوا مناسب است.
برنامه های کاربردی لوله مانیسمان A333 گرید 3/6 در قالب بدون درز و جوش
پالایشگاه ها، نیروگاه ها، بویلرها، ساختمان کشتی، مبدل های حرارتی، مخازن، برنامه های دریایی، نیروگاه های هسته ای، نیروگاه های سوخت فسیلی
لوله های آلیاژی استاندارد لوله ASTM A333 مربوط به لوله های بدون درز و درز دار (جوشی). با آنالیز فولاد آلیاژی و یا کربنی می باشند.
کاربرد لوله های آلیاژی لوله ها در دماهای پایین است. لوله های آلیاژی در چندین گرید مختلف تولید می شوند. لوله ها در دو گروه درز دار و بدون درز تولید می شوند. در لوله های درز دار از فیلرمتال استفاده نمی شود. تمامی لوله های درز دار و بدون درز باید طی یک فرآیند عملیات حرارتی تولیدی و نرمالایز می گردند.
حداکثر مقدار تنش قابل تحمل در لوله های ASTM A333 به شرح زیر می باشد:
TENSILE STRENGTH MIN :GRADE1=MPA.415 PSI.60.000 آزمایش 1-
TENSILE -STRENGTH MIN :GRADE3=MPA.450 PSI.65.000 آزمایش 2-
STRENGTH MIN :GRADE6=MPA.380 PSI.55.000-تنش 3-
موارد کاربرد و تنوع جنس این نوع از لوله ها عبارتند از:
A335-P11 برای محدوده دمایی 400 الی 470 درجه سانتی گراد
پایپ A335-P22 برای محدوده دمایی 400 الی 550 درجه سانتی گراد (هدر های اصلی بخار)
پایپ A335-P91 برای محدوده دمایی 500 الی 560 درجه سانتی گراد
Pipe مانیسمان چیست؟
لوله مانیسمان نوعی از لوله هستند که از بیلت فولادی ساخته می شوند و در بازار به لوله های بدون درز نیز معروف هستند.
بیلت های به کار رفته در لوله مانیسمان گرم و سوراخ کاری می شوند تا مقطع لوله ای شکل ایجاد شود.
به همین دلیل لوله های مانیسمان به لوله های بدون درز نیز معروف و شناخته شده هستند.
کاربرد لوله مانیسمان یا بدون درز
لوله های فولادی بدون درز کاربردهای گسترده ای در صنایع مختلف همچون نفت و گاز هستند.
چند نمونه ازر موارد استفاده این لوله ها در زیر آورده شده است:
- فرایند عملیات بالا دستی (لوله های نفیتی و …)
- عملیات پایین دستی (لوله های مورد استفاده در فرآیندهای تصفیه نفت و گاز)
- عملیات میانی (انتقال و توزیع سیالاتی همچون نفت و گاز و…)
- لوله کشی و تأسیسات
- در خطوط صنایع دارویی و غذایی
- خطوط فشار قوی
- درخطوط نفت و گاز
- خطوط هیدرلیکیانیسمان
رایج ترین لوله های فولادی بدون درز
لوله های فولادی کربنی A53،A333،A106،API 5L از رایج ترین و پرکاربردترین نوع از لوله های بدون درز هستند. که سهم زیادی از بازار را به خود اختصاص دادند.
کاربرد اصلی لوله های فولادی بدون درز شرایطی است. که مقاومت در برابر خوردگی از اهمیت بسیاری برخوردار است. (گریدهای بالاتر از این نوعن لوله ها در مواردی که دما و فشار افزایش می یابند. یا در زمانی که سیال در حال انتقال بسیار خورنده است، استفاده می شوند).
انواع استانداردها
رده بندی استاندارد لوله ها به صورت معمول به صورت های زیر می باشد:
استاندارد: ASME استاندارد لوله های فولادی بدون جوش و بدون درز
استاندارد های :API استاندارد و ویژگی های خط لوله API 5L
ضخامت لوله مانیسمان
لوله های مانیسمان علاوه بر تنوع در سایز با توجه به فشارهای کاری مختلف در ضخامت های مختلفی نیز تولید می شوند.
ضخامت این لوله ها که پیشتر نیز گفته شده، رده لوله نیز گفته می شود.
ضخامت ها نیز بر اساس استانداردهای مختلفی تولید می شوند.
هر یک از رده های 20، 40، 80 از رایج ترین و پر استفاده ترین رده ها می باشند.
لوله مانیسمان رده 20
پایپ رده 20 که معمولاً به عنوان لوله سبک نیز بیان می شود. به عنوان پایین ترین رده شناخته شده در میان انواع رده های لوله های صنعتی می باشد.
لوله مانیسمان رده 40
پایپ رده 40 دارای ضخامت نرمان و استاندارد در لوله ها می باشد. این رده از لوله ها، از لوله های رده 20 قوی تر و از لوله های رده 80 ضعیف تر هستند.
لوله های رده 40 دارای بیشترین استفاده در صنعت هستند.
لوله مانیسمان رده 80
پایپ رده 80 که از ضخامت بالایی برخوردار است، به لوله های سنگین نیز مشهور است.
لوله هایی با رده 80 برای مواردی که فشار کار بالا است. و یا سیال مورد نظر خورندگی بسیار زیادی دارد، مورد استفاده قرار می گیرد.
شرکت خشکه و فولاد پایتخت (( مدیریت : جواد دلاکان )) صنعتگران عزیز، افتخار داریم. که سی سال تجربه گرانبهای خویش را در زمینه عرضه انواع ورق آلیاژی. و انواع فولاد آلیاژی برای خدمت رسانی به شما هموطنان کشور عزیزمان ایران ارائه می دهیم. پیشاپیش از اینکه شرکت خشکه و فولاد پایتخت را جهت خرید خود انتخاب می نمایید سپاسگزاریم.
ارتباط با ما:
۰۹۱۲۱۲۲۴۲۲۷
۰۹۳۷۱۹۰۱۸۰۷
تلفن: ۰۲۱۶۶۸۰۰۲۵۱
فکس: ۶۶۸۰۰۵۴۶